GANRO
HINAKA пневматические и гидравлические цилиндры
Диагностика, Ремонт, Замена шпинделей станков с ЧПУ
Если шпиндель имеет неисправность, наша сервисная служба быстро и эффективно справится с этой проблемой. Но зачем ждать так долго, если проблемы можно обнаружить и устранить заранее?
Наша Диагностика Шпинделей начинается не с неисправности, а с полнофункционирующего шпинделя. На наш взгляд, лучше проводить диагностику во время работы шпинделя и выявлять возможные слабые места. По нашему опыту, 30-40% всех дефектов шпинделей возникают из-за недостаточного или полного отсутствия диагностики и технического обслуживания.
Диагностика шпинделей
С внеаварийной диагностикой шпинделя вы экономите деньги и не нуждаетесь в дорогостоящем ремонте или замене шпинделя, дожидаясь его поломки. Естественно, наша диагностическая работа может быть спланирована точно заранее, чтобы избежать простоев на вашем станке.
Диагностика шпинделя означает, что мы тщательно проверяем состояние подшипников качения и геометрию вашего шпинделя. В некоторых случаях, мы можем обнаружить в шпинделе минимальные отклонения, которые со временем могут стать серьезной проблемой.
Мы также проверяем интерфейс подключения, а также состояние зажима и конус шпинделя. Наша служба шпинделей специализируется на продукции от производителей DMG, Franz Kessler, StepTec, GMN, Royal, Kenturn, Spintech, Posa, Ibag, Fischer, Setco, HSD, Jager, Parker, Weiss, Maina, Gsa, Microlab, SKF. Если потребуется, мы естественно, также будем рады помочь со шпинделями других производителей.
Благодаря регулярной диагностике шпинделей и техническому обслуживанию шпинделя вы достигаете:
- увеличения срока службы шпинделя;
- повышения работоспособности станка;
- повышения производительности и качества;
- раннее распознавание повреждений шпинделя;
- оптимизации процесса механической обработки.
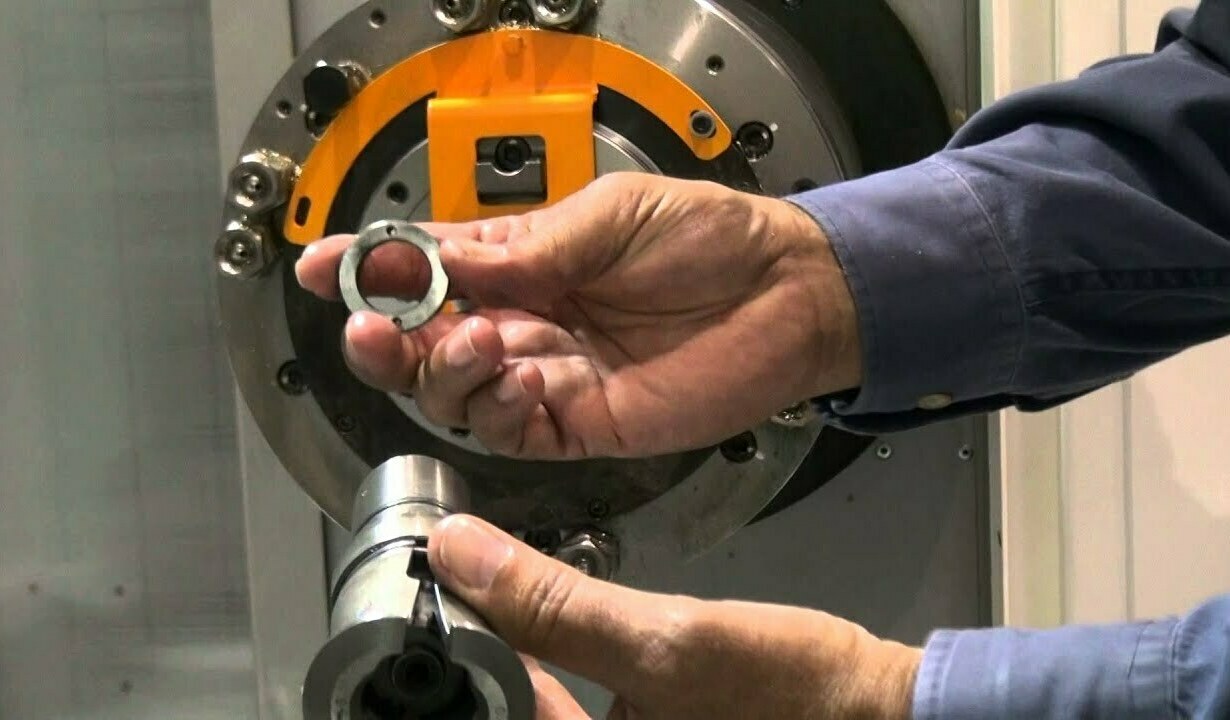
Как мы работаем
Независимо от того, есть ли у вас токарный, фрезерный или шлифовальный ременный или прямой, пневматический и электрический шпиндель или мотор-шпиндель, наши высококвалифицированные сотрудники доведут его до самого высокого уровня производительности, независимо от его производителя.
Мы работаем систематически, эффективно и ориентированны на результат. В качестве первого шага, наши опытные сотрудники определяют фактическое состояние шпинделя и задокументируют его состояние. Если заказчик заключает с нами договор на переборку или ремонт шпинделя, то здесь пора приступать к настоящей работе.
Все отдельные детали шпинедльного узла тщательно очищаются, а дефектные детали заменяются. После этого все детали с вращающимися нагрузками на высоких оборотах уравновешиваются в соответствии с DIN ISO 1940. Сборка отдельных деталей осуществляется с регулировкой всех соответствующих компонентов, таких как преднатяг подшипников, продольная центровка. Вся сборка проводится в кондиционируемом чистом помещении.
После этого производится электрическая регулировка шпинделя. Что включает в себя установку датчиков шпинделя, а также настройку шпинделя на используемые приводы. Прежде чем шпиндель может быть введен в эксплуатацию, мы естественно подвергаем его тщательной и качественной проверке. Мы также можем выполнить полный пуск и настройку кинематики на станке, так как замена шпинделя часто требует оптимизации циклов управления шпинделем. Мы измеряем отклонения во время работы на всех диапазонах и корректируем параметры.
Безразборный метод диагностики шпинделей
С применеием современных средств контроля
Современные методы контроля шпинделей
Повышение Эффективности Производства
Анализатор шпинделя от Automated Precision Inc. (API) - инструмент, используемый при диагностике и обслуживании станков с осью шпинделя. Доступный как Dynamic Analyzer, Thermal Analyzer или комбинированный инструмент, API имеет систему, соответствующую каждому применению.
Анализатор шпинделя гарантирует, что ремонт шпинделя вашего станка не займет больше времени, чем это необходимо, и может помочь сократить время простоя до возникновения проблем.
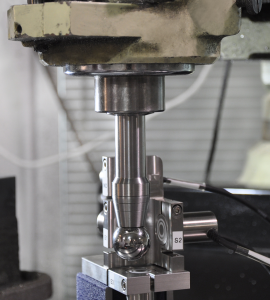
Ваша Система, Ваш Выбор
Если вам нужна система для быстрого измерения ошибок вращения, APIs Spindle Dynamic Analyzer - идеальный инструмент для получения этих данных.
Если вам нужна система для быстрого измерения и контроля кратковременного и долгосрочного теплового роста в 5 степенях свободы (ось X, Y, Z плюс шаг и рыскание), APIs Spindle Thermal Analyzer™ - лучшее решение. То есть, кому требуются обе системы, найдут Apis combination unit идеальным решением.
Использование
- Проверка подшипников;
- Ошибки вращения;
- Осевые погрешности;
- Повторяемость;
- Температурное изменение;
- Сопоставление тепловых ошибок;
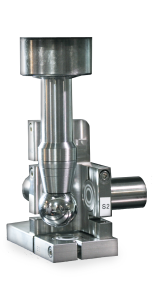
ЯНТАРЬ-М Виброметр с функцией диагностики подшипников
Измерение виброскорости, виброускорения и виброперемещения в стандартных и установленных пользователем частотных диапазонах с заданным временем усреднений.
Возможность сравнения полученных результатов замеров с установленными нормами.
Виброизмерительный прибор ЯНТАРЬ-М (ВУ-043) стал продолжением популярных надежных виброметров ВУ-032, ВУ-034, ВУ-036, выпущенных нашей фирмой с 1990 по 2003 год общим тиражом более 2000 шт.
Использование прибора не требует специальных навыков. Уникальные возможности экспресс-диагностики любых роторных механизмов делают виброизмерительный прибор ЯНТАРЬ-М незаменимым при оценке их технического состояния.
Впервые в приборе подобного класса реализована функция экспресс-диагностики состояния подшипников качения, позволяющая определить наличие зарождающихся дефектов элементов подшипников, а также дефектов монтажа и износа подшипников.
В комплекте с прибором поставляются наушники, позволяющие специалистам производить оценку состояния агрегата по шумам.
Для контроля вибрации и экспресс-диагностики газоперекачивающих агрегатов, нефтяных насосов и другого оборудования, установленного во взрывоопасных помещениях категорий В-1а, В-1б, В-1г, прибор может поставляться во взрывозащищенном исполнении с уровнем взрывозащиты "Повышенная надежность". Маркировка взрывозащиты - 2ExnLIIBT4X.
Зарегистрирован в Госреестре средств измерений № 24386-05
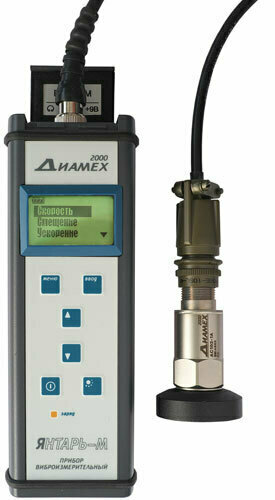
Рычажный индикатор Mahr, длина щупа 14,5 мм
Описание:
Цифровой рычажный индикатор с цифровым и аналоговым дисплеем 1/1000 показаний.
Режим измерения. Нормальный / мин / макс / макс-мин. Можно ввести поправочный коэффициент. Поставляется с: 1 аккумулятор № 081560 размер CR2032, зажимной патрубок ⌀ 8 мм, контактный ключ, твердосплавная контактная точка ⌀ 2 мм. Дополнительное оборудование: Кабель для передачи данных № 498951. Запасные контактные точки см. В № 436210 / 436240.
Калибровка С5
Реверсивное считывание мм / дюйм
IP индекс защиты IP 65
Вид продукции Рычажный циферблат-индикатор
Погрешность гистерезиса fu5 мкм
Диапазон изменения fe10 мкм
Диапазон измерения по направлению 0,4 мм
Корпус ⌀ 43 мм
Длина контактной точки 14,5 мм
Диапазон поворота 2×110 ° градусов
Измерительная сила 0,13 Н
Зажимной хвостовик ⌀ h68 мм
Измерительный шар ⌀ 2 мм
Артикул № батареи / перезаряжаемой батареи, установленной 081560 CR2032
Количество содержащихся батарей 1
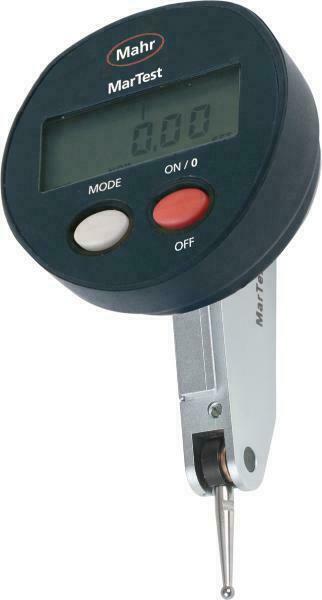
OTT-JAKOB Power-Check 2 и комплект оправок (SK 40, SK 30, HSK 63А)
В технологии станкостроения контроль силы втягивания как часть обеспечения качества имеет важное значение для того, чтобы гарантировать стабильно точные результаты обработки.
Уменьшенное усилие зажима может оказать долгосрочное воздействие.
Низкое качество поверхности из-за вибраций
Повышенный износ инструмента и более короткий срок службы инструмента.
Коническая коррозия шпинделя, вызванная микродвижениями
Поломка инструмента
Простой станка
Риск травмирования оператора станка
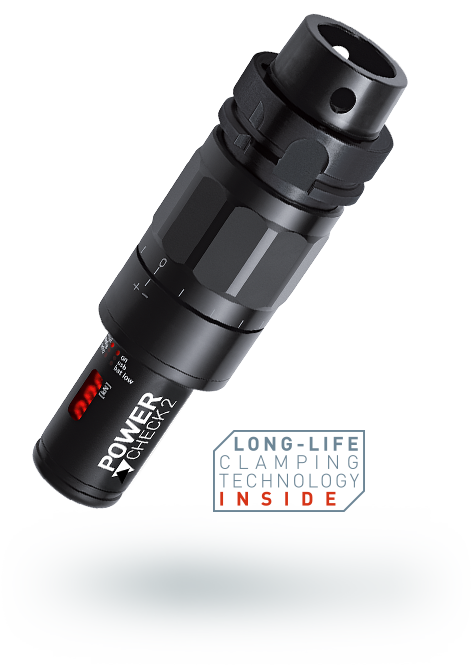
Список оборудования и инструментов для диагностики шпиндельных узлов на станке.
- Оправка контрольная для проверки радиального биения DIN 69871 SK40 х 40 х 312 мм
- Оправка контрольная для проверки радиального биения HSK 63A х 40 х 364 мм
- Мобильный тепловизор Seek Thermal
- Виброметр с функцией диагностики подшипников Диамех Янтарь-М
- Рычажный индикатор Mahr, длина щупа 14,5 мм. Цена деления 1/1000 мм
- Светодиодный фонарь с питанием от аккумулятора
- Набор отверток
- Магнитная стойка 3-мерная измерительная шарнирная h=210 мм (радиус действия 130 мм)
- OTT-JAKOB Power-Check 2 и комплект оправок (SK 40, SK 30, HSK 63А)
Вибро диагностика шпинделей
На основе исследований колебаний в металлорежущих станках показано, что применение современной виброизмерительной аппаратуры и датчиков, в частности трехкомпонентных датчиков вибраций, увеличивает точность измерений, значительно расширяет возможности вибрационного анализа, позволяет оценивать траекторию колебательного движения, получать аттракторы (самовозбуждающиеся колебания в контуре с положительной обратной связью) и диагностировать на этой основе наличие и величину дисбалансов, качество монтажа и состояние подшипниковых узлов и несущей системы станков.
Постоянно растущие требования к надежности технологического оборудования автоматизированного производства выдвигают на первый план необходимость получения и анализа информации о состоянии узлов и механизмов оборудования, о состоянии инструмента, заготовок, о протекании процесса обработки [1, 2]. Наиболее удобным для целей диагностики является вибрационный сигнал, который получается с датчиков вибраций – акселерометров. Современные средства для измерения абсолютных колебаний, например, такие как трехкомпонентные датчики вибрации, позволяют получать информацию о состоянии механизма в наиболее полном виде. Анализ информации о вибрационном состоянии оборудования может производиться не только по величине суммарной виброскорости, амплитуде и фазе оборотной гармоники (как это принято в практике виброисследований [3]), но и по траектории движения измеряемой точки в плоскостях и пространстве, и по формам колебаний конструкции в целом [4, 5].
Применение трехкомпонентных датчиков вибрации уменьшает трудоемкость работ по сбору информации. Так, одним датчиком за один замер можно получить вибрационные характеристики сразу по трем направлениям (осям), что при обычном способе измерений (три однокомпонентных датчика) порой не представляется возможным в силу конструктивных особенностей объекта изучения. Применение датчиков нового типа увеличивает точность измерений, поскольку наличие одного чувствительного элемента напрямую влияет на качество представления информации о вибрационном состоянии изучаемого объекта.
В работе [6] показано применение трехкомпонентных датчиков вибрации для диагностики процесса обработки на станках, для оценки состояния режущего инструмента и заготовок. Говоря о диагностике непосредственно оборудования, в частности таких наиболее ответственных узлов станков, как шпиндельные, следует отметить, что за рубежом методы вибродиагностики широко распространены [7, 8]. Они составляют основу любой системы технического мониторинга и часто функционально объединены с системами автоматического управления. Например, шпиндельные узлы фирм «GF Agie Charmilles», «Mazak», «DMG Mori», «Hermle» оснащены не только датчиками температуры, но и стационарными акселерометрами. С их помощью контролируется уровень вибраций при обработке. Сигналы с акселерометров можно использовать для диагностики состояния опор шпинделя.
Простейший контроль шпиндельного узла может опираться на статистические характеристики вибросигнала, взятого в том или ином частотных диапазонах. Это среднеквадратичное значение (СКЗ), пиковое значение, пик-фактор (отношение пикового значения к СКЗ), эксцесс [9]. Все эти параметры несут информацию об общем состоянии подшипникового узла, но с их помощью нельзя конкретизировать причину повышенной вибрации. Предварительные исследования шпиндельных узлов на стадии обкатки и мониторинг в процессе эксплуатации могут выявить те вибрационные параметры, за которыми надо следить и нормировать в первую очередь.
Подшипники, в которых установлен шпиндель, в значительной степени определяют состояние всего узла и являются источником вынуждающих сил. Колебания в подшипнике качения порождаются несовершенной геометрией его элементов, силами трения и ударными импульсами, создаваемыми телами качения (шариками или роликами).
В качестве примера предлагается рассмотреть результаты исследований двух одинаковых шлифовальных шпинделей на подшипниках качения. На рис. 1 показаны спектры виброакустических (ВА) сигналов в радиальном направлении, полученных с помощью трехкомпонентного акселерометра. На рис. 1 (а) показан спектр виброускорений шпинделя № 1, который после часовой обкатки на 9000 об./мин имел температуру нагрева корпуса в месте установки передних подшипников на 15 градусов ниже по сравнению со шпинделем № 2, спектр виброускорения которого приведен на рис. 1 (б). Из этих спектров видно, что у шпинделя № 2 резко повышена амплитуда составляющих в районе 4,5 кГц. Это говорит о более интенсивном фрикционном взаимодействии подшипниковых колец в шпинделе № 2 с телами качения.

Рисунок (а)
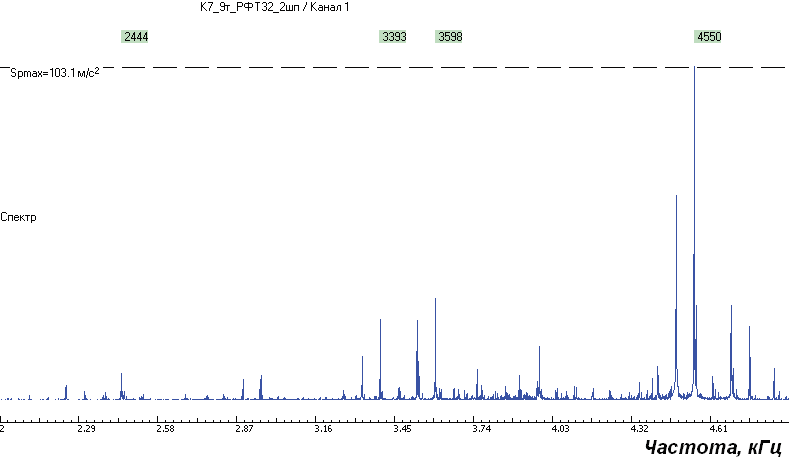
Рисунок (б)
Рис. 1. Спектры виброускорений корпуса шпинделя при частоте 9000 об./мин по оси Y для шпинделя № 1 (а) и шпинделя № 2 (б)
При применении методов ВА диагностики к анализу состояния подшипников традиционно применяется метод спектрального разложения огибающей высокочастотного ВА сигнала. На рис. 2 представлены подобные разложения для двух шпинделей. Для построения огибающей из регистрируемого ВА сигнала с помощью полосового фильтра была выделена составляющая в диапазоне от 2.8 до 5.6 кГц. Далее по программе сигнал разбивался на временные интервалы (величина интервала определялась требуемым частотным диапазоном спектрального разложения), для каждого из которых определялось эффективное значение амплитуды, в результате получалось дискретное представление огибающей, которое затем разлагалось в спектр. На рис. 2 (а) представлен спектр огибающей для шпинделя № 1, а на рис. 2 (б) – для шпинделя № 2. На обоих спектрах видно по три основных составляющих, которые проявляются на пер- вой, второй и третьей частотах вращения сепаратора относительно наружного кольца. Это может говорить об износе тел качения и о перекосе подшипниковых колец друг относительно друга при сборке шпиндельного узла. В работе [3] говорится, что момент сил сопротивления вращению подшипника аналогичен характеру и амплитудам колебаний, вызываемых заеданием в сепараторе. В приведенном примере в обоих шпинделях проявляются колебания, связанные с враще- нием сепаратора, однако видно, что у вто- рого шпинделя амплитуда этих гармоник в несколько раз больше, чем у шпинделя № 1.

Рисунок (а)
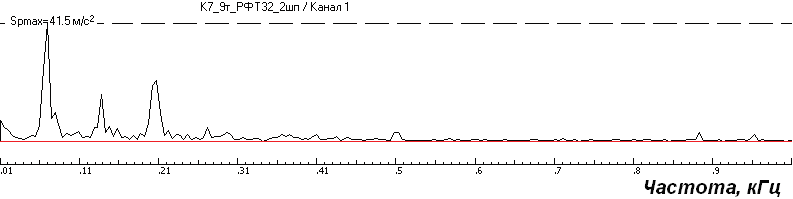
Рисунок (б)
Рис. 2. Спектры огибающей ВА сигнала со шпинделя № 1 (а) и шпинделя № 2 (б) в октавной полосе со средней геометрической частотой (СГЧ) 4 кГц при частоте вращения 9000 об/мин
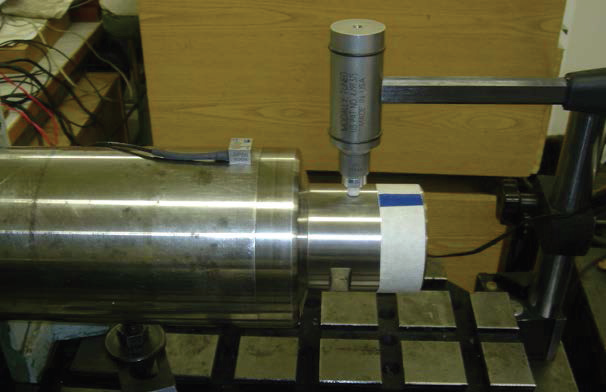
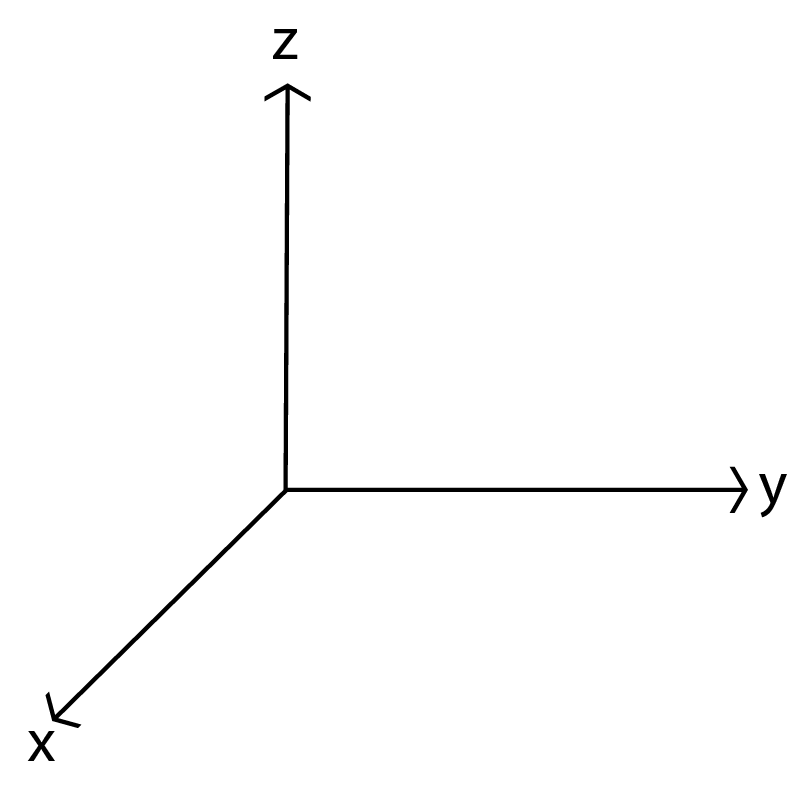
Рис. 3. Импульсное нагружение шпинделя и измерение реакции трехкомпонентным акселерометром
Качеству диагностики опор шпинделя могут способствовать амплитудно-частотные характеристики (АЧХ), полученные экспериментально, например, с помощью импульсного нагружения шпинделя [10, 11] (рис. 3). Такие характеристики мало применялись непосредственно к диагностике подшипников.
На рис. 4 показаны АЧХ шпинделя № 2, построенные по двум взаимно перпендикулярным осям. Акселерометр устанавливался на корпусе шпинделя. Динамометрическим молотком наносились удары по концу шпинделя в радиальном направлении. Вектор импульсного воздействия и ось акселерометра лежат в одной плоскости, проходящей через ось шпинделя.
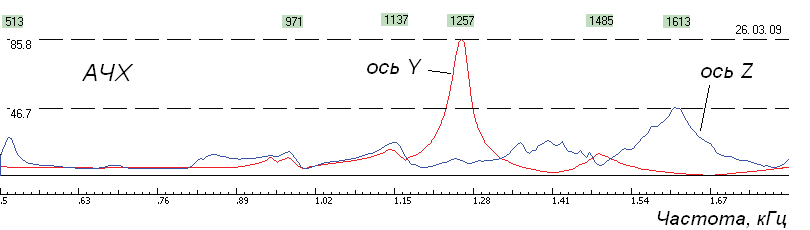
Рис. 4. АЧХ шпинделя № 2 по осям Z и У
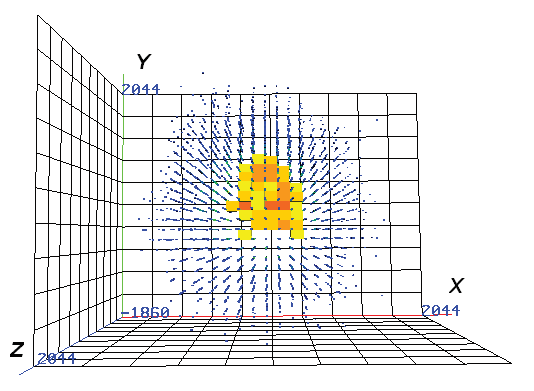
Рис. а
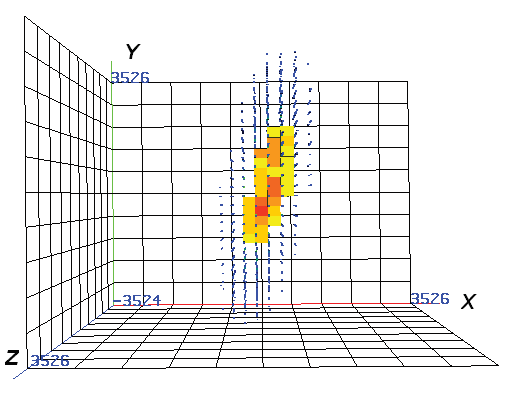
Рис. б
Рис. 5. Объемное изображение колебаний в октаве с СГЧ 4 кГц со стороны оси Z: а – шпиндель № 1; б – шпиндель № 2.
В идеальном случае АЧХ не должны существенно зависеть от выбора плоскости расположения ударного импульса и акселерометра. На рис. 4 показаны АЧХ, постро- енные для вертикальной (ось Z) и горизонтальной (ось У) плоскостей. Видно, что в направлении оси У податливость, особенно в районе частоты 1257 Гц, значительно выше, чем податливость по оси Z. Это можно трактовать как следствие неравномерного радиального натяга в подшипнике, вызванного искажением радиальной геометрии при посадке колец.
Построение АЧХ дает полезную информацию о состоянии подшипникового узла [12, 13], но такая методика связана с необходимостью применения динамометрического молотка, который может отсутствовать на предприятии. Информацию о качестве работы шпинделя можно получить, подключая к стенду для обкатки шпинделя трехкомпонентный датчик вибраций, с помощью которого можно следить за поведением вектора виброускорения, виброскорости или виброперемещения по направлению координатных осей. На рис. 5 показаны примеры пространственного представления распределения вибраций при холостом вращении шпинделей на 9 000 об./мин. На рис. 5 (а) показано пространственное распределение колебаний в диапазоне 2,8 – 5,6 кГц для шпинделя № 1. Цветом выделено ядро распределения. В этих ячейках пространства вектор колебаний присутствует основное время. В других частях пространства, обозначенных точками, вектор колебаний тоже бывает, но реже. Для сравнения на рис. 5 (б) показано аналогичное пространственное распределение для шпинделя № 2. Ось Х изображения совпадает с осью шпинделя, ось Z шпинделя расположена вертикально и перпендикулярна оси шпинделя, ось У шпинделя расположена горизонтально.
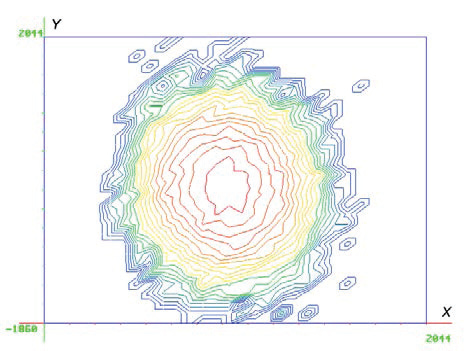
Рис. а
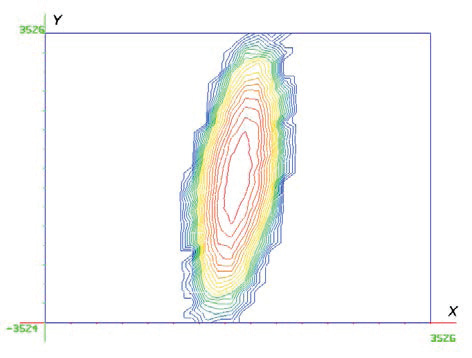
Рис. а
Рис. 6. Двумерные законы распределения вероятности присутствия вектора колебаний в точках плоскости ХОУ: а – шпиндель № 1; б – шпиндель № 2
Обращает на себя внимание тот факт, что пространственное изображение колебаний шпинделя № 2 имеет больший (почти в 2 раза) разброс позиций вектора в пространстве и большую вытянутость распределения вдоль оси У. Это подтверждает вывод, сделанный с помощью анализа АЧХ. Таким образом, большая податливость порождает большой разброс высокочастотных колебаний. Соответственно, по форме и размаху пространственного изображения можно судить о ряде недостатков шпиндельного узла. На рис. 6 показаны примеры представления колебаний, полученных с трехкомпонентного акселерометра, стоящего на корпусе шпинделя по осям У и Z. Здесь время присутствия вектора колебаний в точках пространства изображено линиями равного уровня. По сути, это изображение проекций распределения, показанного на рис. 5 на плоскость УZ. Показанные на рис. 6 (а) и рис. 6 (б) два изображения для шпинделей № 1 и 2 по аналогии с рис. 5 показывают рост размаха колебаний и вытянутости по оси У у шпинделя № 2 по сравнению со шпинде- лем № 1.
Выше указывалось, что шпиндель № 2 при прогоне в течение часа на 9000 об./мин показал температуру на корпусе вблизи передней опоры на 15 градусов выше, чем шпиндель № 1 при аналогичных условиях. Надо отметить, что такой относительный прирост температуры не вывел его за пределы нормы, он был признан годным к эксплуатации. Однако из приведенных данных экспериментов видно, что полученные в результате анализа параметры ВА сигнала у шпинделя № 2 заметно отличаются. Это говорит о высокой чувствительности параметров ВА сигнала к изменению состояния шпиндельного узла.
Дальнейшие задачи разработчиков методов ВА диагностики в приложении к оценке качества шпиндельных узлов состоят в определении границ изменения диагностических параметров, полученных с помощью различных представлений ВА сигнала [9]. Но основная трудность лежит на пути установления связей тех или иных несоответствий, возникающих в процессе изготовления шпиндельного узла с изме- нением одного или нескольких параметров ВА сигнала. На первых порах можно опираться на методики ВА диагностики состояния подшипников, но они не могут в полной мере отражать особенности шпин- дельного узла. Это и наличие собственных форм изгибных колебаний шпинделя [14], и изменение натяга с ростом темпе- ратуры [15], и значительно более высокие скорости вращения шпиндельного узла по сравнению со стандартными скоростями испытания самих подшипников [16]. Так, например, радиальная амплитуда колебаний на частоте вращения при увеличении угловой скорости с 2 000 об/мин до 11 000 об/мин может увеличиться в десятки раз. На рис. 7 и рис. 8 показаны спектры виброускорения шпинделя фрезерного станка мод. 6М13, зафиксированных при разных числах оборотов. На рис. 7 скорость вращения была 2 000 об/мин, на рис. 8, эта скорость составляла 11 000 об/мин. Видно, что на малых оборотах в спектре практически отсутствует амплитуда на оборотной частоте, видны только ее вторая и третья гармоники. На больших оборотах картина меняется, на спектре доминирует первая гармоника, ее амплитуда несоизмеримо возрастает.
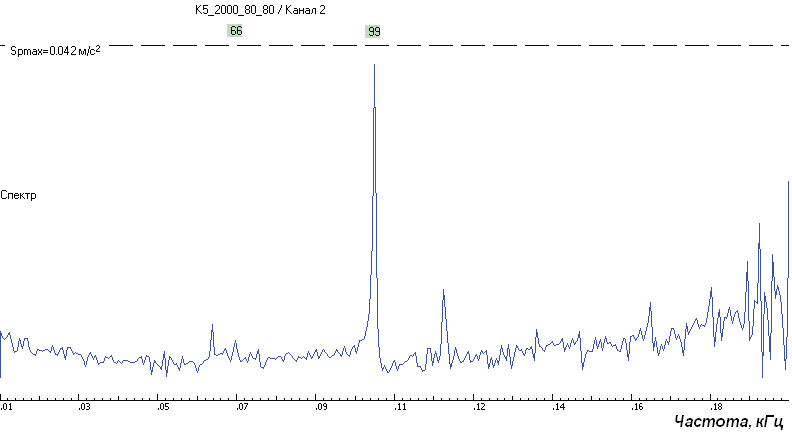
Рис. 7. Спектр колебаний корпуса шпинделя по оси У (по нормали к плоскости направляющих) при 2000 об/мин. Частота 66 Гц соответствует второй гармонике оборотной частоты, 99 Гц – третья гармоника
На рис. 9 с помощью линий равного уровня показано распределение колебаний корпуса шпинделя в плоскости ХОУ в районе передней опоры при 11 000 об/мин. Видно, что по оси У присутствуют редкие, но значительные по амплитуде отклонения шпинделя от плоскости направляющих.
Дело в том, что отклонения от идеальной модели присутствуют всегда. Это перекосы колец подшипников, некруглость дорожек качения, остаточный дисбаланс шпинделя и т.п. Степень проявления этих отклонений в параметрах ВА сигналов зависит от числа оборотов, величины и направления нагрузок, действующих на шпиндель в процессе рабочего цикла.
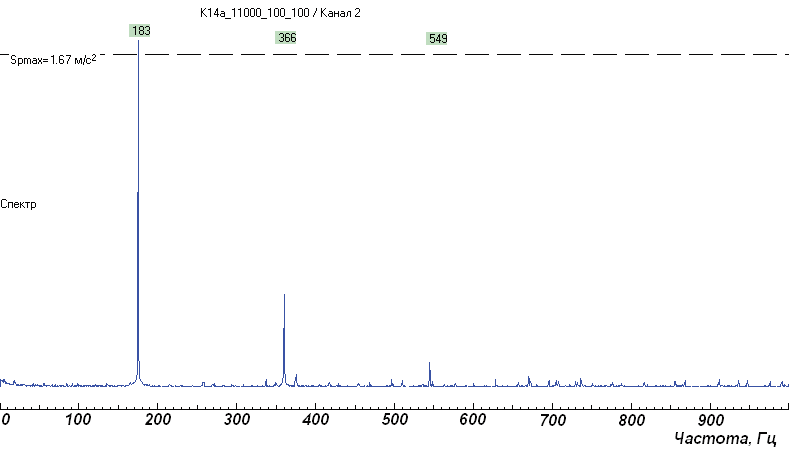
Рис. 8. Спектр виброускорения по оси У шпинделя на 11 000 об/мин. Видны 1-я, 2-я и 3-я гармоники оборотной частоты
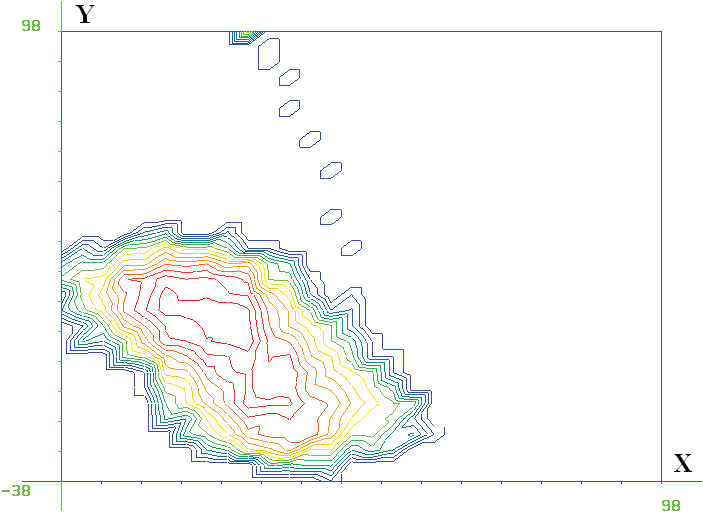
Рис. 9. Распределение колебаний шпинделя в плоскости ХОУ на 11 000 об/мин. Ось Х параллельна направляю- щим, ось У перпендикулярна плоскости направляющих. Видно, что по оси У присутствуют кратковременные от- клонения шпинделя от плоскости направляющих
Представляется, что перечисленные в данной статье проблемы, решение которых можно осуществлять с помощью трехкомпонентных датчиков вибраций и анализа аттракторов, не исчерпывают всех направлений возможных исследований, количество которых может увеличиваться по мере совершенствования процедур регистрации и анализа фазовых траекторий.
Сервис шпинделей станков
Сервис шпинделей
Мы занимаемся восстановлением всех шпинделей. Наши процессы ремонта шпинделей стали передовыми в своем деле. У нас есть современные внутренние ресурсы и обученные техники и сервисные инженеры, так что ваш отремонтированный шпиндель будет лучше, чем новый, когда мы отправим его вам.
Что еще более важно, мы имеем полный доступ к деталям, а также полные производственные возможности, что позволяет нам правильно отремонтировать шпиндель вашего станка с первого раза.
Услуги по восстановлению и диагностика шпинделей
Наши специалисты тщательно проверяют шпиндель, чтобы правильно определить проблему, прежде чем приступить к любым работам по ремонту шпинделя. Все шпиндели подвергаются следующей 5-этапной оценке:
1. Анализ входящих вибраций
Анализ поступающих вибраций проводится с целью определения: состояния подшипников, уровня дисбаланса и/или любых других частот дефектов, которые могут существовать и негативно влиять на работу шпиндельного узла.
2. Осмотр собранного шпинделя
Биение конуса на конце инструмента и посадочного места выполняется для определения возможной аварии шпинделя или неправильной установки инструмента. Осмотр биения задней конусности для определения возможного излишнего затягивания ремней или неправильной посадки шкива. Испытание под нагрузкой для определения износа подшипников или аварии шпинделя.
3. Осмотр демонтированного шпинделя
Осмотр конусности для определения аварии шпинделя, неправильнй установки инструмента или перегрева. Проверка цапфы подшипника для определения неправильной посадки подшипника или использования шпинделя после первоначального отказа. Общее состояние вала для определения аварии, перегрева, отсутствия охлаждающей жидкости или перегрузки.
4. Состояние подшипников
Проверка подшипников проводится квалифицированными специалистами по подшипникам для определения отсутствия смазки, превышения скорости поломки шпинделя, перегрузки, потери предварительного натяга, загрязнения (попадания охлаждающей жидкости или другого материала) или перегрева из-за электрических проблем. Кроме того, у нас есть доступ ко всем представителям и дилерам производителя подшипников.
5. Технические рекомендации
Мы рекомендуем внести изменения или усовершенствования в конструкцию шпинделя для повышения долговечности и/или производительности шпинделей. Например, если шпиндель вышел из строя из-за загрязнения, будет рекомендовано и реализовано изменение конструкции, такое как - установка нового лабиринтного уплотнения, продувка воздухом, установка гибридных подшипников или улучшение конструкции уплотнения.
Что мы предлагаем
Шпиндель нужно извлечь из станка. Удаление может быть сделано либо самим заказчиком, либо нашими специалистами, которые могут быть отправлены на завод клиента для демонтирования шпинделя.
Ремонт
После планирования ремонта шпинделя выдаются корректирующие действия, восстановление, а также рекомендации по профилактическому обслуживанию, о которых необходимо позаботиться перед установкой шпинделя обратно в станок.
Тестирование
Шпиндели испытываются, чтобы проверить, все ли части интерфейса станка работают исправно, такие как энкодеры, бесконтактные переключатели и т. д. Все должно функционировать должным образом, и все шпиндели должны пройти анализ вибрации.
Установка шпинделя на станок
После ремонта шпинделя производится установка на станок и проверка на работоспособность и надежность, которая может быть выполнена по требованию заказчика нашим специалистом.
Результаты работ
Мы любим эту не простую командную работу по ремонту шпинделей. Смотрите сами на возрождения шпинделей ниже, это результаты профессионализма и тщательных ремонтных работ, посмотрите на широко представленное разнообразии брендов, с которыми мы работаем. Независимо от того, что случилось с вашим шпинделем, мы стремимся сделать его лучше, чем новый.
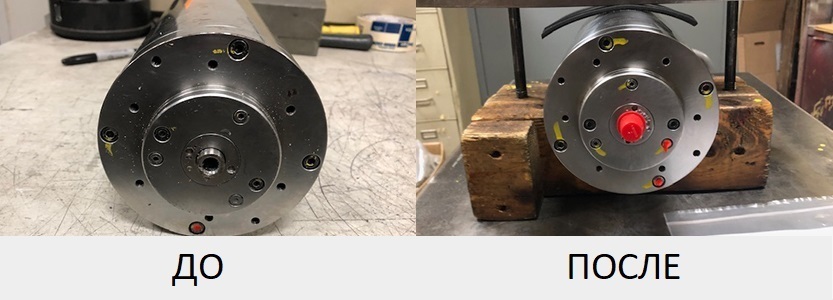
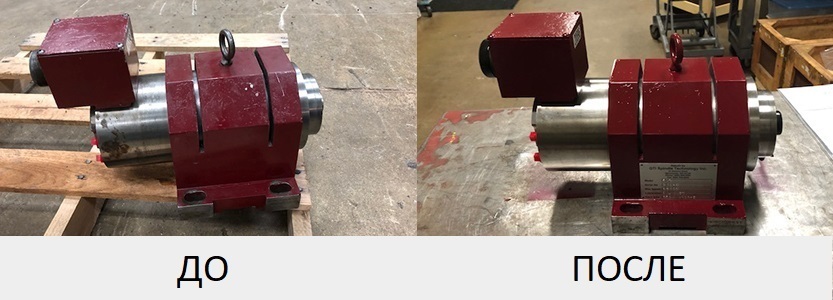
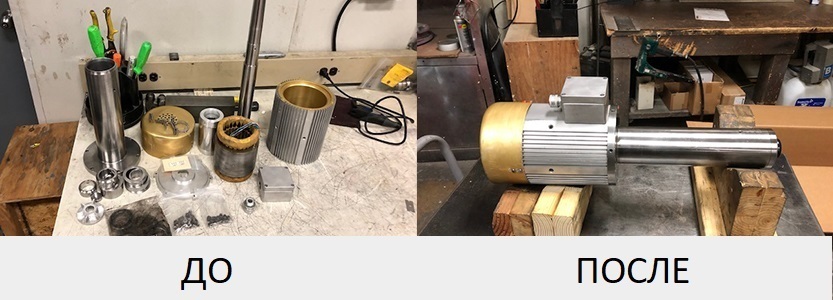
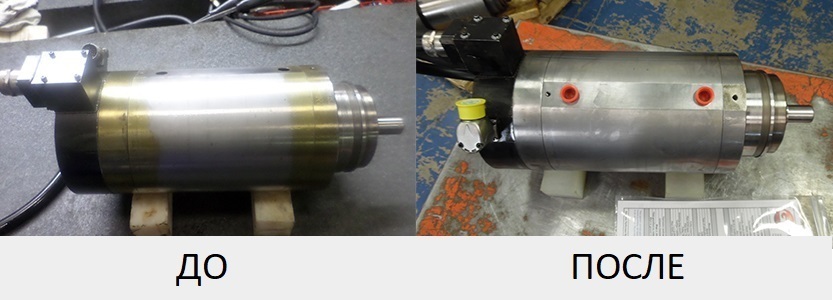
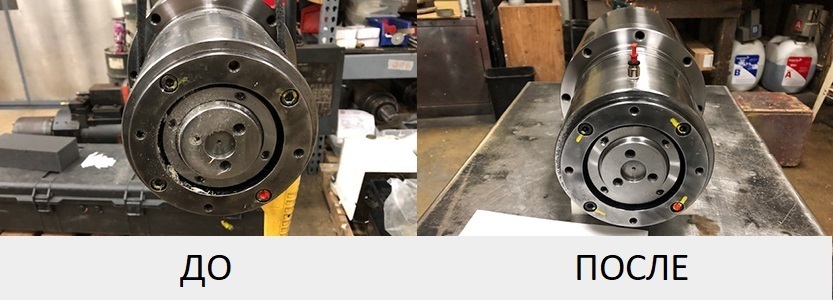
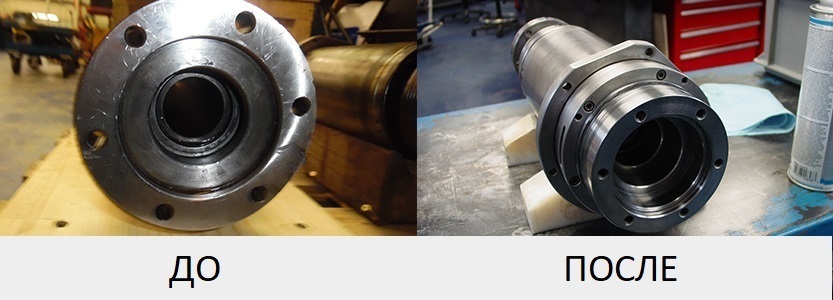
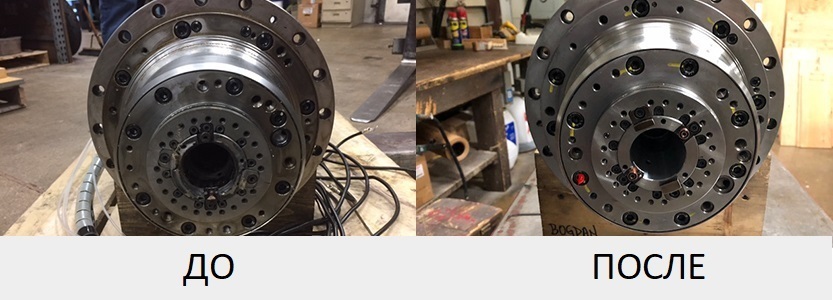
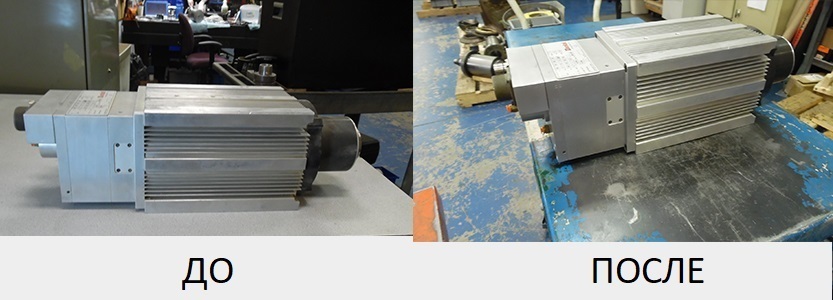
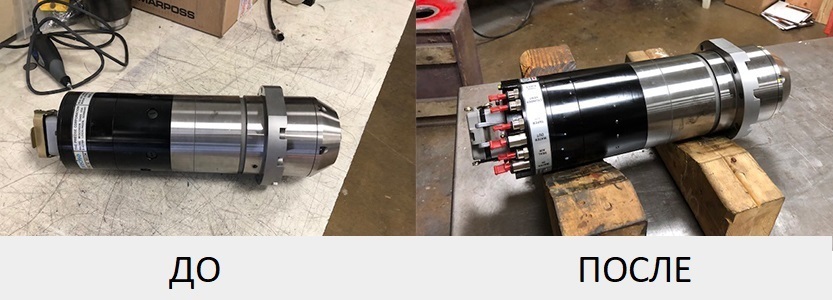
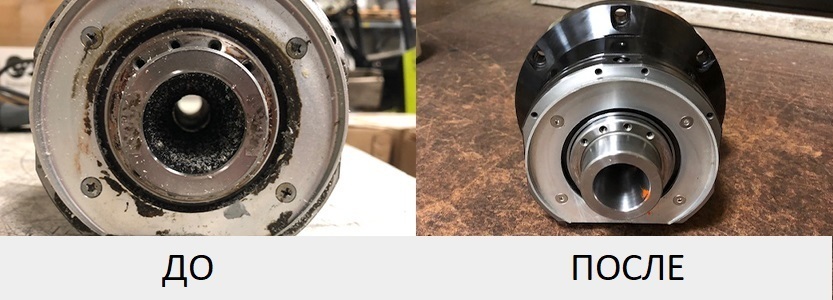
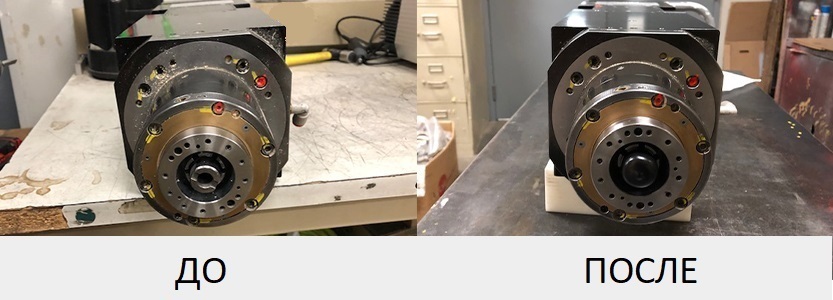
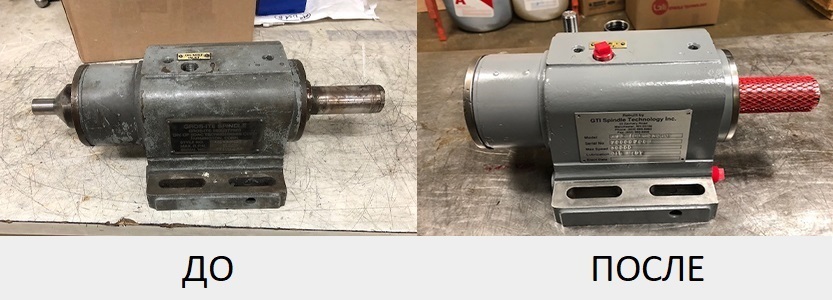
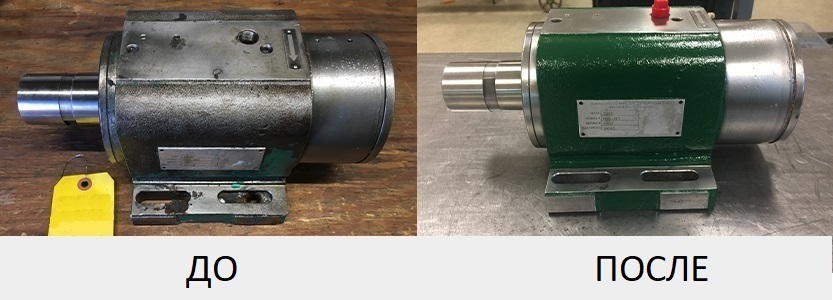
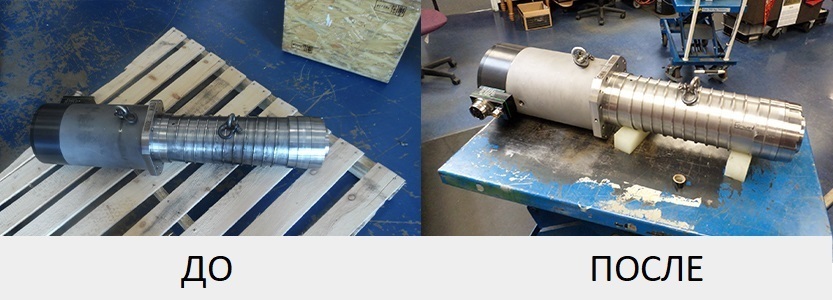
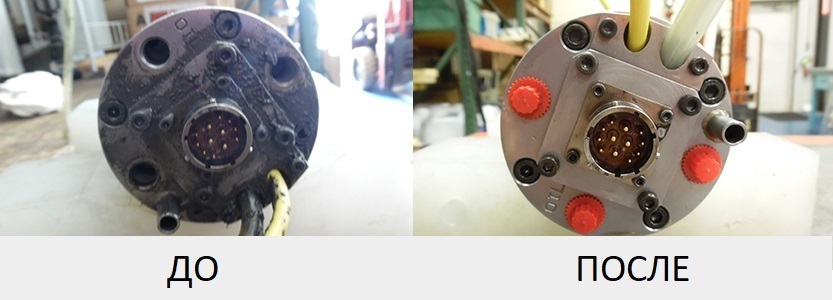
Abrasive
ABA
Accretech
Accu Router
Acer
Acroloc
Adcock & Shipley
Advanced Controls
Advanced Machine
Aerotech
Aetna
Agathon
AGT
Alfing
Alfred Jaeger
Alpine
Alzmetall
American Precision Spindles
Ameri Seiki
Anayak
Anca
Anderson
Ansaldo
APS
Arcadini Machine
Argo Seiki
Arter
Asahi
ASC
Ashai
ASV
ATI
Atlas
Atrump
Auerbach
Axa
Axiome
Axxiom
Bahmuller
Barber Coleman
Barnes
Baumuller
Bavelloni
Bayer
Behr
Benchman
Berger
Berthiez
Bertoni & Cotti
Bertsche
Biesse
Bima
Blake
Blanchard
Blohm
Blombach
Boehringer
Boneham
Boneham & Turner
B & T
Bostomatic
Bowen
Boyar Schultz
Brembana
Breton
Bridgeport
Brio
Brother
Brown & Sharpe
Bryant
BSI
Buffoli
Buhr
Bullard
Burkhardt Weber
Busellato
BWF
Campbell
Canton
Capellini
Cargil
Carlton
Carver
Celoschi
Centerline
Centreline
Chevalier
Chiron
Churchill
Cincinnati
Cincinnati Lamb
Cinex
Citizen
Clausing
Cleerman
Cleveland
CME
CMS Brembana
Coborn
Coburn
Colchester
Colmatic
Colonial
Colombo
Comau
Combing
Comec
Covel
Cross Huller
Cyclone
Cytec
Cy-tec
Dac
Daewoo
Dah Lih
Dainichi
Danieli
Dankaert
Danobat
Darbert
Dearborn
Deckel Maho
Delta
Demer
Denzo
Dependable
Deuschle
Devlieg Bullard
Diebold
Diedesheim
DKFL
DMG
DMH
Doall
Doosan
Dorries Scharmann
Drake
Dresser
Droop Rein
DRR
DS Technologie
Dumore
Dunham
Dynomax
Dynamotion
E2 Systems
Ekstrom Carlson
ELB Schliff
Eldorado
Elliott
Elmo
Elox
Elte
Emag
Emco Famup
Emco Maier
Engis
Enshu
Enzfelder
Erem
Erfurt
Everite
Eumach
Euroma
Eurotech
Ewag
Excel
Excello
Ex-Cell-O
Excellon
Fadal spindle
Faemat
FAG
Fair Friend
Falcon
Falva
Fam Costruzioni
Fanuc
Fastems
Favretto
Federal Mogul
Feeler
Felker
Fellows
Femco
Femina
Fidia
First
Fischer AG
Fischer Precision
FM Eurospindle
FMN
FMT Group
FM Umbra
Fortuna
Fortune Victor
Fosdick
FPS
FPT
Franz Kessler
Frauenthal
Fritz Studer
FS
Fuji
GA
G&L
Galaxy
Gallmeyer & Livingston
Gamfior
Gardner
Giddings & Lewis
Gildemeister
Gilman
Giordano Colombo
Gioria
Gleason Pfauter
Gleason Works
GMN
GMS
Gomiya
Goodway
Goratu
Gorton
Graziano
Grisetti
Grob
Gros-ite
Grosite
GTI
Guhring
Haas
Hamai
Hamal
Hammond
Handtmann Machining
Hardinge
Harig
Haril
Harvill
Hatchi
Hauser
H & D
Heald
Heathway
Hedelius
Heian
Heinz Fiege
Heller
Hemburg
Hemple
Hendrick
Henninger
Herbert Lindner
Herbold
Hermle
Hertlein
Hessapp
High Speed Technologies
Hillyer
Himmel
Hitachi
Hitachi-Seiki
Hoborough
Holzma
Homag
Horton
HSD
HST
Huffman
Huller Hille
Hurco
Huron
Hwacheon
Hybco
Hydromat
Hyundai
Ibag
Ihara
Ikegai
IMA America
IMA Techno
IMC
IMF
IMP
IMT
Impco
Incor
Index
Indramat
Ingersoll
Innse Berardi
Intermac
Invinceable
Ionic
Iwata
Jaeger
Jager
J&L
Jackmill
Jakobsen
Japan
Jet
Jobs
Johanson
Johnford
Joisten & Kettenbaum
Joke
Jones & Lamson
Jones & Shipman
Jung
Jungner
Kapp
Kamenicek
Karstens
KaVo
KO Lee
Kao Ming
Kasper
Kasuga
Kearney & Trecker
Keighley
Kenturnlong
Kellenberger
Keller
Kennard
Kent
Kenward
Kessler
Ketterer
Kia
Kikinda
Kindt-Collins
Kingsbury
Kira
Kitagawa
Kitako
Kitamura
Kiwa
Klingelnberg
Kolb
Kollmorgan
Komo
Kondia
Korber
Kovosvit
Koyo
Kruger
Kummer
Kuraki
Lagar
Lagun
Lamb
Landis
Lasalle
Leach
Leadwell
Le Blond
Leblond Makino
Lenz
Levicron
Lian Feng
Lidk Ping
Liebherr
Lima
LincoLinea
LMT Lidkoping
Lodge & Shipley
Loewe
LOH GMN Maag
Louis Allis
Lucas
Lumley
Maag
Magnaghi
Magerle
Maho
Makino
Maltech
Mandelli
Manex
Mania
Mao Ling
Marubeni Citizen-Cincom
Masco
Master
Master Setco
Matec
Matrix Churchill
Matsuura
Mattison
Mauser
Maut
Max Rawyler
Mazak
McDonough
Meccanica Cortini
Meccanica Nova
Mecof
Meiden
Menlo
Micromatic
Mighty
Mikron
Mikrosa
Milltronics
Millport
Minganti
Mitek
Mitsubishi
Mitsui Seiki
Miyano
Mizoguchi
MMS
Modig
Monarch
Monoset
Moore
Morbidelli
Mori Seiki
Motch
Motionmaster
MPA
Multiax
Multicam
Murata
Muratec
Mutter
M W Hydralink
Myford
MYL
Nakamura Tome
Nardini
Neo
New Britain
New Century
Newall
Niagara
Nicco
Nichols
Nicolas Correa
Nigata
Niigata
Niles
Nippee
Nippei
Nippon
Nishida
Nissin
Nomura
Normac
Northland
Northwood
Norton
NSK
NSP
NTC
NTN
Noberg
Oberg
Oerlikon
Officine Biglia
Officine Paventa
Okamoto
OKK
Okuma
Okuma & Howa
Oliver
Oloffson
O.L.M.A.
OMC
OMG
Omlat
OMV
OMZ
Onsrud
Ooya
Orcutt
Orion
Overbeck
Paatz
Pama
Parker Majestic
Parpas
PBA Spindles
PBS
PDA
Peron Speed
Perske
Piat
Pietro Carnaghi
Pittler Kessler
Pluritec
Point
Pokolm
Pope
Pope Setco
Porta
Porter
Posa
Posalux
Pratt & Whitney
Precimax
Precise
Precision Balancing and Analyzing
Profimat
Puma
Quantum
Quickmill
R&B
RAS
RO
Rambaudi
Ransburg
Reckerth
Red Head
Reid
Reinecker
Reishauer
Rema Control
Renaud
Renault Automation
Rettificatrici Ghiringhelli
Ribon
Riello Sistemi
Rigid
Rivett
Rockwell
Roku Roku
Romai
Romi
Ronos
Ross
Routech
Royal Oak
Rudel
Rush
Rye
Saeilo
Saginaw
Sachman Rambaudi
Saimp
Sakazaki
Samp
Samsung
Savway
SchaudtSchleifring
Schmid
Schmoll
Schneider
Schussler
Schutte
Schwabische Werkzeugmaschinen
SCM
Scripta
Seiko Seiki
Sema
Seneca Falls
Serrmac
Setco
SFJ
Sharnoa
Shaper
Sheffield
Shigiya
Shin Oh
Shinko
Shinks
Shino
Shizouka
Shoda
SHW Werkzeugmaschinen
Siarto
Sicar
Siemens AG
Siga
Sigma
Simav
Simplex
Sintex
SIP
Sirmec
Sjogren Saginaw
SKF
Slamco
SLF
Smart & Brown
SMG
SMS
SMZ
SNK
Snow
Somex
Sopko
Spandau
Spintec
SPL
Springfield
Stama
Standard
Stanko
Star
Starrag Heckert
Stefani
StepTec
Sticker
Stoffel
Strausak
Studer
Sugino
Summit
Sunmax
Sun Tool
Sunnen
Sunstrand
Supermax
Swifter
Swisher
Swiss Lathe
SycoTec
Synchron
TAC
Tacchella Macchine
Taft Pierce
Tai-Chin
Taisei
Tajmac-ZPS
Takisawa
Takumi
Taurus
TDM-SA
Techint Pomini
Technica
Tecnometal
Tekna
Tempo
Tenco
Themac
Thermwood
Theta Precision
Thibaut
Thompson
Thor
Tongil
Tongtai Seiki
Tong Yi
Topper
Tornos
TOS
Toshiba
Toyama
Toyo Kogyo
Toyoda
Traminer
Traub
Tree
Tripet
Trudrill
Truflute
Tschudin
Tsugami
Tulon
Umbra
Urben
Ulam
UltraTurn
Union
Unison
Universal Automatic
UVA
VEM
Van Norman
Victor
Vigel
Vollmer
Voumard
Vulcanaire
Wadkin
Wagner
Waida
Waldrich Coburg
Waldrich Siegen
Walter
Ward
Wardell
Warner-Swasey
Wasino
Wedalco
Weeke
Weinig
Weiss
Weisser
Weldon
Wendt
Wessel
Whacheon
Wheelabrator
White-Sunstrand
Whitnon
Wickman
Wickman-Sheffield
Willemin
Winslow
Wirth & Gruffat
Wit-O-Matic
Woods
Woodtronic
Wotan
Woton
Yachyio
Yamage
Yamaguchi
Yamashida
Yamazaki
Yang
YCI
Yeong Chin
Zaro Macchine
Zayer
Ziersch & Baltrusch
Zocca
Zuber